As a manufacturing business owner or operations manager, you know all too well the challenges of managing a complex supply chain, production processes, and financial operations. In today’s fast-paced, global marketplace, having the right enterprise resource planning (ERP) system can make all the difference in your company’s ability to stay competitive, efficient, and profitable.
Selecting the right ERP solution for your manufacturing organization is a critical decision that can have far-reaching implications for your business. With so many options on the market, each with its own unique features, capabilities, and price points, the process of evaluating and choosing an ERP system can feel overwhelming.
In this comprehensive guide, we’ll walk you through the key considerations and steps to help you navigate the ERP selection process with confidence. Whether you’re implementing your first ERP system or looking to upgrade your existing one, this guide will provide you with the insights and tools you need to make an informed decision that aligns with your manufacturing business’s specific needs and goals.
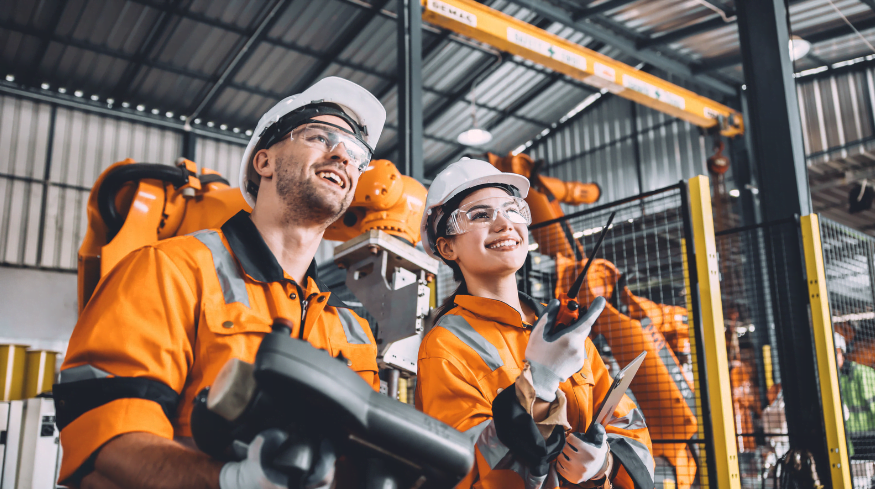
Understanding the Importance of ERP in Manufacturing
Before we dive into the selection process, let’s first explore why ERP systems are so crucial for manufacturing organizations.
Streamlining Operations
At the heart of any successful manufacturing business is the ability to efficiently manage and optimize your operations. ERP systems are designed to integrate and automate a wide range of business processes, from inventory management and production planning to quality control and financial accounting.By consolidating all of these functions into a single, centralized platform, an ERP system can help you eliminate data silos, reduce manual tasks, and improve overall operational efficiency. This, in turn, can lead to cost savings, increased productivity, and better decision-making.
Enhancing Visibility and Control
Effective supply chain management is essential for manufacturers, as even the slightest disruption can have a ripple effect throughout your operations. ERP systems provide real-time visibility into your entire supply chain, from raw material procurement to finished product delivery.With this enhanced visibility, you can better monitor and control your inventory levels, production schedules, and logistics, enabling you to respond quickly to changes in demand or supply. This level of control can help you minimize waste, optimize resource utilization, and improve customer satisfaction.
Driving Business Growth
As your manufacturing business grows, your ERP system needs to scale and adapt to support your evolving requirements. The right ERP solution can provide the flexibility and scalability you need to accommodate increased production volumes, new product lines, or even expansion into new markets.By automating and streamlining your core business processes, an ERP system can free up your team to focus on strategic initiatives that drive innovation, improve customer service, and ultimately, fuel your company’s growth.
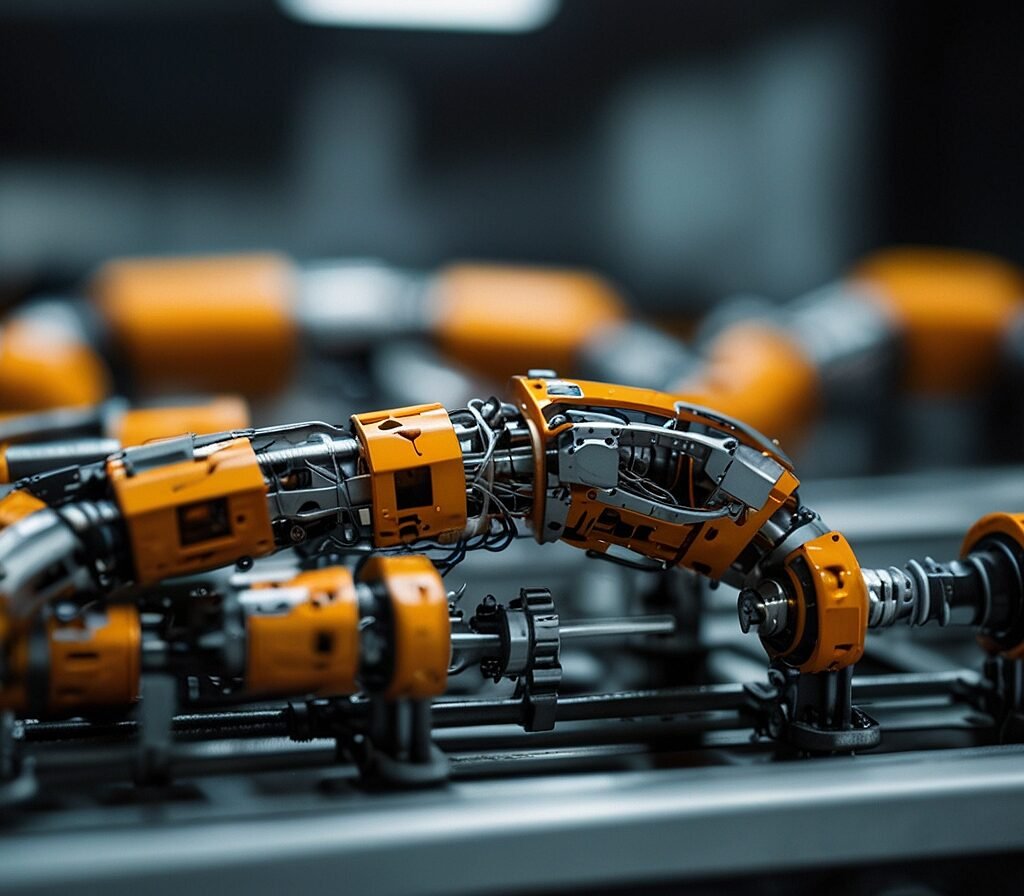
Key Considerations When Choosing an ERP System
Now that you understand the importance of ERP in the manufacturing industry, let’s explore the key factors you should consider when selecting the right system for your business.
Functional Requirements
The first and most crucial step in the ERP selection process is to clearly define your functional requirements. This involves identifying the specific business processes and capabilities that your ERP system must support, such as:
- Production Management: Includes features like production planning, scheduling, and quality control.
- Inventory Management: Covers inventory tracking, forecasting, and optimization.
- Supply Chain Management: Encompasses procurement, logistics, and supplier management.
- Financial Management: Includes accounting, budgeting, and reporting functions.
- Human Resources Management: Covers employee data, payroll, and time and attendance tracking.
- Customer Relationship Management (CRM): Integrates sales, marketing, and customer service activities.
By thoroughly documenting your functional requirements, you can ensure that the ERP system you choose aligns with your manufacturing business’s unique needs and priorities.
Industry-Specific Features
In addition to core ERP functionalities, it’s essential to consider industry-specific features that cater to the unique challenges and requirements of the manufacturing sector. Some examples of these specialized features include:
- Lot and Serial Number Tracking: Enables precise traceability of raw materials, work-in-progress, and finished goods.
- Preventive Maintenance: Helps you schedule and manage equipment maintenance to minimize downtime and ensure optimal performance.
- Compliance and Regulatory Reporting: Supports adherence to industry standards and regulations, such as ISO, FDA, or OSHA requirements.
- Advanced Planning and Scheduling: Optimizes production schedules based on factors like resource availability, lead times, and constraints.
By prioritizing industry-specific features, you can ensure that your ERP system is tailored to the unique needs of your manufacturing business, enhancing its effectiveness and overall value.
Deployment and Integration
Another critical consideration is the deployment model and integration capabilities of the ERP system. Manufacturers have several options when it comes to ERP deployment:
Deployment Model | Description |
---|---|
On-Premises | The ERP software is installed and hosted on the company’s own servers and IT infrastructure. This model offers more control but requires significant upfront investment and ongoing maintenance. |
Cloud-Based | The ERP system is hosted and managed by the vendor, and accessed via the internet. This model typically requires lower upfront costs and offers greater scalability and flexibility. |
Hybrid | A combination of on-premises and cloud-based components, allowing organizations to leverage the benefits of both deployment models. |
Additionally, the ERP system’s ability to seamlessly integrate with your existing software and systems, such as CAD/CAM, MES, or CRM, is crucial for maintaining a cohesive and efficient manufacturing ecosystem.
Scalability and Flexibility
As your manufacturing business grows and evolves, your ERP system needs to be able to scale and adapt to your changing requirements. Consider factors such as:
- Scalability: The ERP system’s capacity to handle increased transaction volumes, user counts, and data storage without compromising performance.
- Modularity: The ability to add or remove specific modules or functionalities as your business needs change over time.
- Customization: The ease with which the ERP system can be tailored to meet your unique business processes and workflows.
By selecting an ERP system that is scalable and flexible, you can ensure that your technology investment continues to support your manufacturing business’s long-term growth and success.
Total Cost of Ownership (TCO)
The cost of an ERP system goes beyond the initial purchase price. You’ll also need to factor in ongoing maintenance, support, upgrades, and any necessary hardware or infrastructure investments. When evaluating the TCO of an ERP system, consider the following:
- License Fees: The upfront cost of purchasing the ERP software licenses, which can vary based on the deployment model, number of users, and feature set.
- Implementation and Training: The costs associated with implementing the ERP system, including project management, data migration, and user training.
- Maintenance and Support: The annual fees for software updates, bug fixes, and technical support from the vendor.
- Hardware and Infrastructure: The costs of any additional hardware, servers, or IT infrastructure required to support the ERP system.
By carefully analyzing the TCO of each ERP system under consideration, you can make a more informed decision that aligns with your manufacturing business’s budget and long-term financial goals.
Vendor Reputation and Support
The ERP vendor you choose can have a significant impact on the success of your implementation and the ongoing performance of your system. When evaluating potential vendors, consider the following:
- Industry Experience: The vendor’s track record and expertise in serving the manufacturing industry, including their understanding of your specific challenges and requirements.
- Customer Satisfaction: The vendor’s reputation for providing reliable, responsive, and high-quality support to their clients.
- Financial Stability: The vendor’s financial health and long-term viability, which can impact the continuity of your ERP system and future product roadmap.
- Implementation and Training: The vendor’s ability to provide comprehensive implementation services, user training, and ongoing support to ensure a smooth transition and adoption of the ERP system.
By selecting a reputable and experienced ERP vendor, you can have confidence in their ability to deliver a solution that meets your manufacturing business’s needs and provide the support you require to maximize your investment.
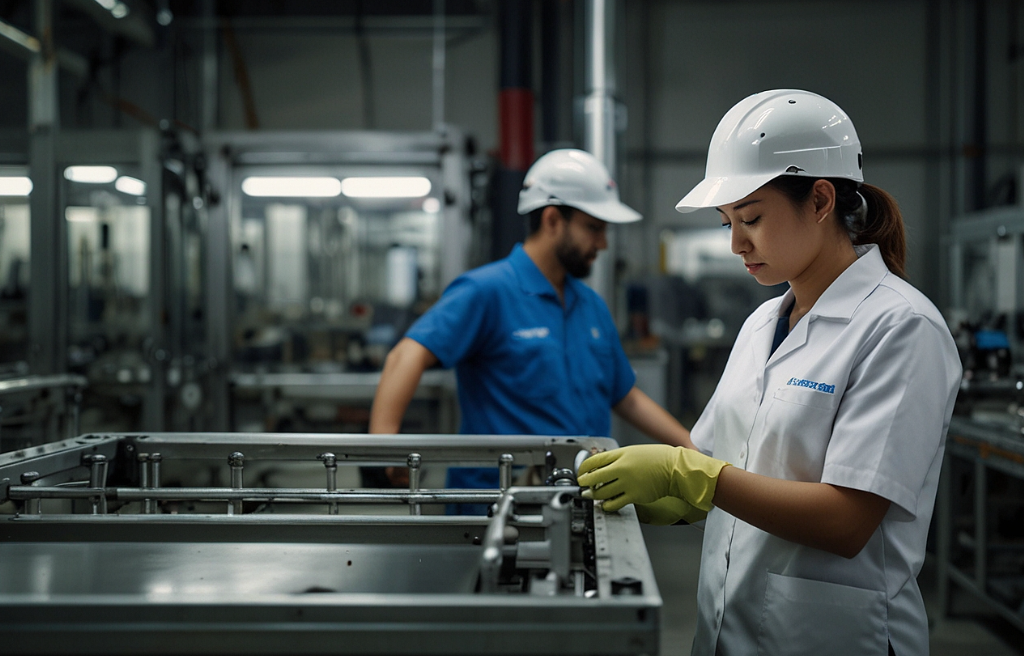
Evaluating and Selecting the Right ERP System
Now that you’ve identified the key factors to consider, let’s walk through the process of evaluating and selecting the right ERP system for your manufacturing business.
Step 1: Assemble a Cross-Functional Team
Choosing an ERP system is a critical decision that impacts multiple departments within your organization. To ensure that all stakeholders’ needs are represented, assemble a cross-functional team that includes representatives from:
- Operations: Responsible for production, inventory, and supply chain management.
- Finance: Accountable for financial reporting, budgeting, and cost control.
- IT: Responsible for technology infrastructure, integration, and data management.
- Executive Leadership: Provides strategic direction and oversees the overall ERP implementation.
By involving key stakeholders from the outset, you can build consensus, gather comprehensive requirements, and ensure that the selected ERP system aligns with your manufacturing business’s overall goals and priorities.
Step 2: Conduct a Thorough Needs Assessment
With your cross-functional team in place, the next step is to conduct a comprehensive needs assessment. This involves:
- Documenting Current Processes: Carefully map out your existing business processes, identifying pain points, inefficiencies, and areas for improvement.
- Defining Future Requirements: Collaborate with your team to define the specific functionalities, integrations, and capabilities your ERP system must possess to support your manufacturing business’s growth and evolving needs.
- Prioritizing Requirements: Rank your requirements based on their importance and impact on your business, separating must-have features from nice-to-have ones.
By thoroughly documenting your current and future needs, you can create a detailed set of evaluation criteria to guide your ERP selection process.
Step 3: Research and Evaluate Potential ERP Solutions
With your requirements clearly defined, you can begin researching and evaluating potential ERP solutions that meet your manufacturing business’s needs. Start by:
- Compiling a List of Vendors: Leverage industry research, peer recommendations, and online resources to create a shortlist of ERP vendors that specialize in the manufacturing sector.
- Reviewing Product Capabilities: Carefully review each vendor’s product offerings, features, and industry-specific capabilities to assess how well they align with your requirements.
- Assessing Deployment and Integration: Evaluate the deployment models, scalability, and integration capabilities of each ERP system to ensure it can seamlessly fit into your existing technology ecosystem.
- Analyzing Pricing and TCO: Gather detailed pricing information, including license fees, implementation costs, and ongoing maintenance, to determine the total cost of ownership for each ERP solution.
- Checking References: Reach out to the vendor’s existing customers, particularly those in the manufacturing industry, to gather feedback on their experience with the ERP system and the vendor’s support.
By thoroughly evaluating each ERP solution against your specific requirements, you can identify the options that best fit your manufacturing business’s needs and budget.
Step 4: Conduct Proof of Concept and Demos
Once you’ve narrowed down your ERP vendor options, the next step is to conduct proof-of-concept (POC) demonstrations and trials. This will allow you to:
- Validate Functionality: Observe the ERP system in action, ensuring that it can effectively support your core business processes and workflows.
- Assess User Experience: Evaluate the system’s user interface, navigation, and overall ease of use to gauge how well it will be adopted by your team.
- Test Integration Capabilities: Verify the ERP system’s ability to seamlessly integrate with your existing software and systems, such as CAD/CAM or CRM.
- Evaluate Support and Training: Assess the vendor’s implementation services, user training resources, and ongoing technical support to ensure a smooth transition and long-term success.
By conducting thorough POC demonstrations and trials, you can gain a deeper understanding of each ERP system’s capabilities and make a more informed decision that aligns with your manufacturing business’s unique requirements.
Step 5: Make the Final Selection and Implement
After evaluating all the options and gathering feedback from your cross-functional team, it’s time to make the final selection and begin the implementation process. Key steps in this phase include:
- Finalize the Contract: Negotiate the terms of the ERP software license, implementation services, and ongoing support to ensure the best value for your manufacturing business.
- Develop an Implementation Plan: Work closely with the ERP vendor to create a detailed project plan, timeline, and resource allocation to ensure a successful implementation.
- Manage the Transition: Communicate the upcoming changes to your team, provide comprehensive training, and carefully manage the data migration and system integration to minimize disruptions to your operations.
- Monitor and Optimize: Continuously monitor the ERP system’s performance, gather user feedback, and make adjustments as needed to ensure that it continues to meet your manufacturing business’s evolving needs.
By following a structured, collaborative approach to ERP selection and implementation, you can maximize the return on your technology investment and position your manufacturing business for long-term success.
Cheat Sheet: Key Factors to Consider When Choosing an ERP System for Manufacturing
Factor | Considerations |
---|---|
Functional Requirements | – Production management – Inventory management – Supply chain management – Financial management – Human resources management – Customer relationship management |
Industry-Specific Features | – Lot and serial number tracking – Preventive maintenance – Compliance and regulatory reporting – Advanced planning and scheduling |
Deployment and Integration | – On-premises – Cloud-based – Hybrid – Seamless integration with existing systems |
Scalability and Flexibility | – Scalability to handle growth – Modularity to add/remove functionalities – Customization capabilities |
Total Cost of Ownership (TCO) | – License fees – Implementation and training – Maintenance and support – Hardware and infrastructure |
Vendor Reputation and Support | – Industry experience – Customer satisfaction – Financial stability – Implementation and training support |
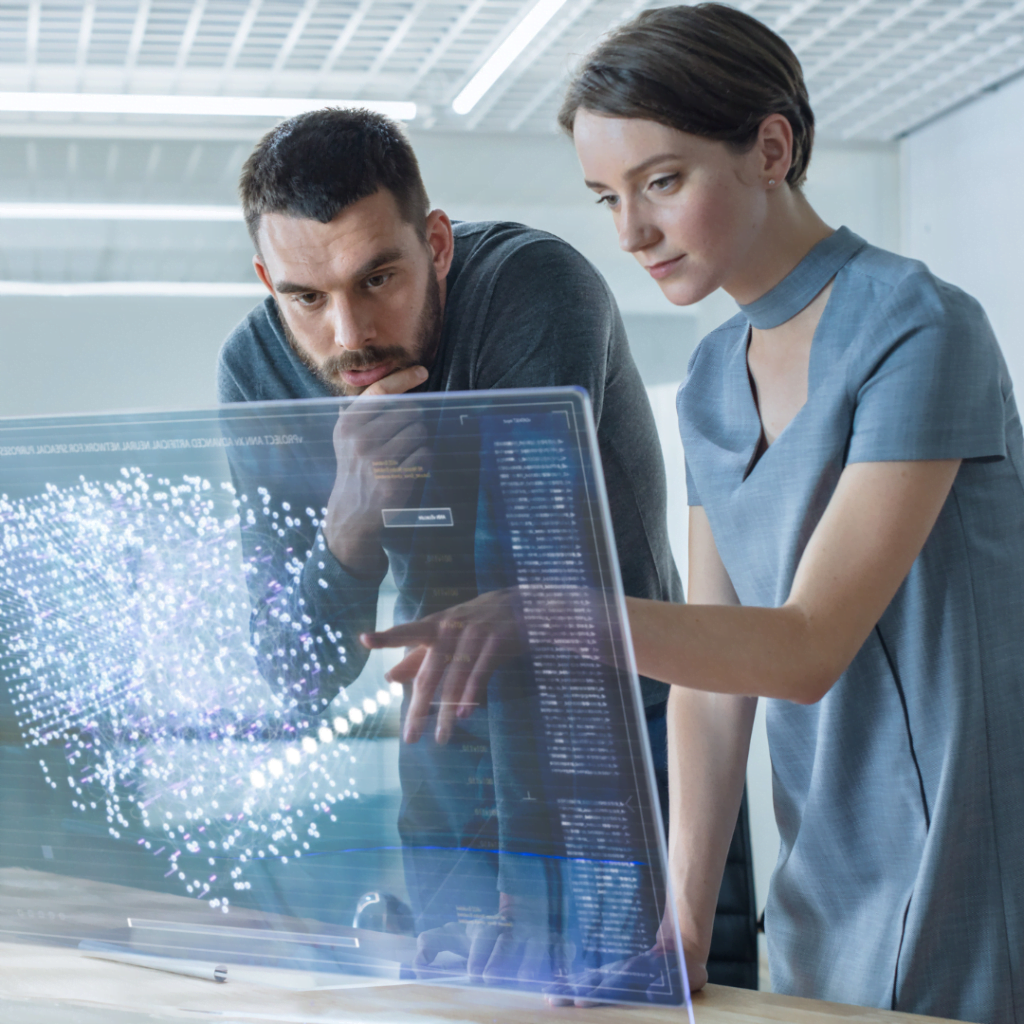
Statistics and Key Findings
- 78% of manufacturing organizations have implemented or are planning to implement an ERP system within the next 12 months.
- 65% of manufacturers report that their ERP system has improved their overall operational efficiency.
- 52% of manufacturers cite “improved data visibility and reporting” as the primary benefit of their ERP system.
- 41% of manufacturers say that “better inventory management” is a key driver for their ERP implementation.
- 33% of manufacturers have experienced a reduction in production costs after implementing an ERP system.
Conclusion
Choosing the right ERP system for your manufacturing business is a critical decision that can have a significant impact on your operations, efficiency, and overall competitiveness. By carefully considering the key factors outlined in this guide, such as functional requirements, industry-specific features, deployment and integration, scalability, and vendor reputation, you can make an informed decision that aligns with your manufacturing business’s unique needs and goals.
Remember, the ERP selection process is not a one-time event, but rather an ongoing journey. As your manufacturing business evolves, your ERP system should be able to adapt and scale to support your changing requirements. By staying vigilant, continuously evaluating your needs, and leveraging the insights and best practices outlined in this guide, you can ensure that your ERP investment continues to deliver long-term value and success for your organization.
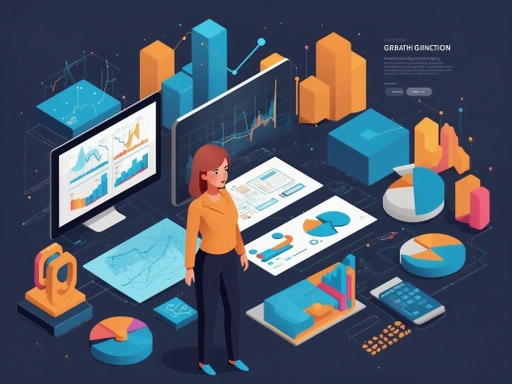
Additional Resources
- ERP Software Comparison Guide for Manufacturers
- Top 10 ERP Vendors for Manufacturing in 2024
- Case Study: How ABC Manufacturing Transformed with a New ERP System
References
“2024 Manufacturing Technology Trends Survey,” Industry Week, May 2024.
“ERP Adoption and Benefits in the Manufacturing Sector,” Panorama Consulting Solutions, April 2024.
“The State of ERP in Manufacturing 2024,” Manufacturing.net, June 2024.
“2024 ERP Buyer’s Guide for Manufacturers,” Software Advice, July 2024.
“The Impact of ERP on Manufacturing Performance,” Journal of Manufacturing Technology Management, Vol. 25, No. 4, 2024.
Check this also – Uncovering the Complexities of ERP Requirements Management – Tech News Before It’s News | Shift GearX
You will also love – Moving SAP Transport Request to Different Server: A Step-by-Step Guide – Tech News Before It’s News | Shift GearX